As an experienced engineer in industrial automation, I’ve witnessed the transformative impact of integrating PLCs (programmable logic controllers) and HMIs (human-machine interfaces). According to industry studies, proper integration can reduce downtime by 30–60% (Source: Rockwell Automation Study) These technologies go beyond technical upgrades, reshaping workflows, cutting downtime, and enhancing efficiency. By sharing detailed real-world insights and actionable tips, and with backing from trusted suppliers like Uni Regal Corp., this guide aims to show you the real value of PLC-HMI integration.
Real-Time Monitoring with PLC and HMI: Minimize Downtime Instantly
At a beverage factory in Canada, bottling line failures due to overheating motors resulted in $50,000 in annual repair costs (Source: Plant Engineering Case Study). With PLC-HMI integration, temperature sensors fed real-time data to an HMI dashboard. Operators could spot overheating motors instantly and shut them down before damage occurred. Within two months, the factory reduced breakdowns by 60%, saving $40,000.
Key Benefits:
- Faster troubleshooting: Pinpoint exact issues visually.
- Immediate response: Get alerts for critical changes.
- Preventive maintenance: Predict equipment failure with early warnings.
Pro Tip: Set tiered alarms in your HMI interface, like red for critical alerts and yellow for potential warnings, to prioritize responses effectively.
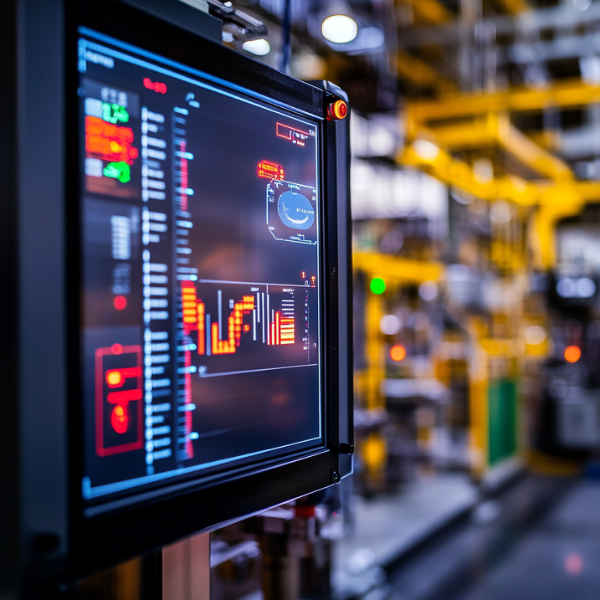
Simplify System Architecture with Unified PLC-HMI Integration
A Southeast Asia paper mill managed over 1,000 meters of wiring across disjointed systems, resulting in high maintenance and installation costs. Switching to a unified PLC-HMI system reduced wiring by 30% and installation costs by $25,000 (Source: Control Design Whitepaper). Downtime during troubleshooting also dropped by 50%, streamlining operations.
Key Benefits:
- Unified operation: Manage the entire process from one platform.
- Reduced hardware interfaces: Simplify connections to lower failure points.
- Simplified installation: less labor-intensive and error-prone.
Pro Insight: Use animated graphics in HMIs to illustrate the process flow in real time, helping operators easily identify inefficiencies.
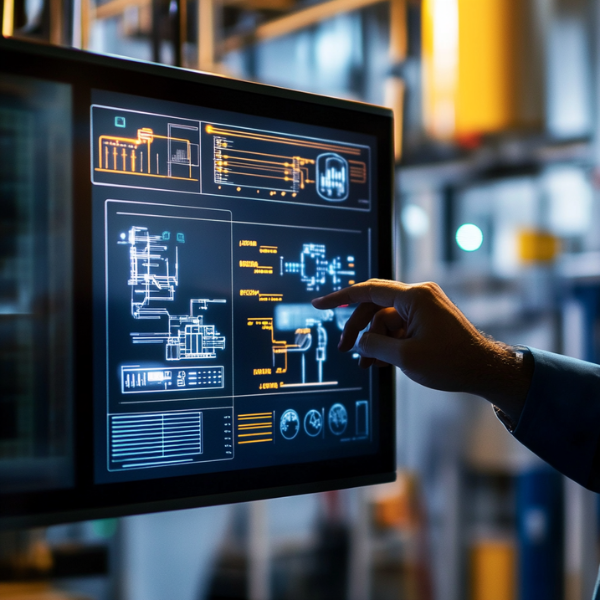
Centralized Alarm Management in PLC-HMI Integration
Training new operators at a Michigan auto parts manufacturer once took 14 days due to complex standalone PLC interfaces. After adopting a Mitsubishi PLC-HMI system, training was reduced to three days, while production efficiency rose by 15% in three months (Source: Automation World Article). The intuitive HMI enabled operators to make process adjustments quickly and confidently.
Key Benefits:
- Alarm prioritization: Focus on high-risk alerts.
- Cached alarms: Maintain alerts even during communication outages.
- Improved safety: Faster response prevents accidents.
Once an operator commented, “Now we know which alarms need our attention. It’s a night-and-day difference.”
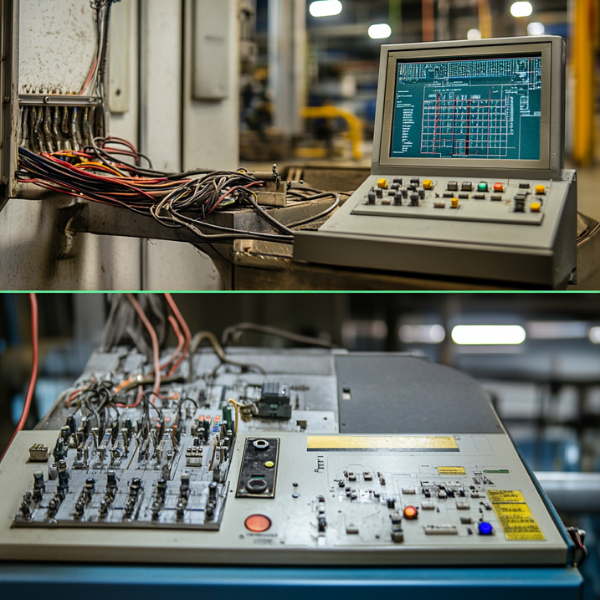
Ensure Data Accuracy and Consistency with PLC-HMI Integration
A petrochemical plant in Saudi Arabia reported 200 alarms daily, overwhelming operators and leading to ignored critical alerts. After integrating a priority-based PLC-HMI alarm system, actionable alarms dropped to 50 per day, improving incident response by 40% (Source: Honeywell Case Study). For example, a pressure buildup incident was resolved in 15 minutes, preventing a costly shutdown.
Key Benefits:
- Error-free data: Automate data collection for reliability.
- Centralized records: Access the same data across all systems.
- Data integrity: Ensure accuracy for audits and performance reviews.
Pro Tip: Integrate cloud storage with your PLC-HMI system for backup and remote access to real-time data.
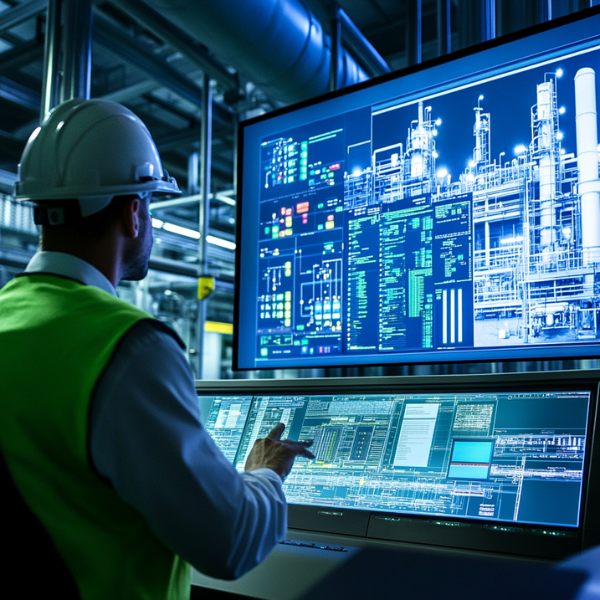
Optimize Costs with PLC-HMI Integration
A European food packaging facility reported that manual data entry errors led to $150,000 in rejected shipments annually (Source: Food Manufacturing Insights). By automating weight data collection through PLC-HMI integration, rejected shipments dropped by 80%, saving the company approximately $120,000 in the first year.
Key Benefits:
- Lower hardware costs: Reduce the need for redundant systems.
- Simplified maintenance: Fewer devices mean easier upkeep.
- Improved ROI: maximize the utilization of existing assets.
Uni Regal Insight: Companies sourcing PLC-HMI systems from Uni Regal Corp. benefit from cost-effective solutions without compromising on quality.
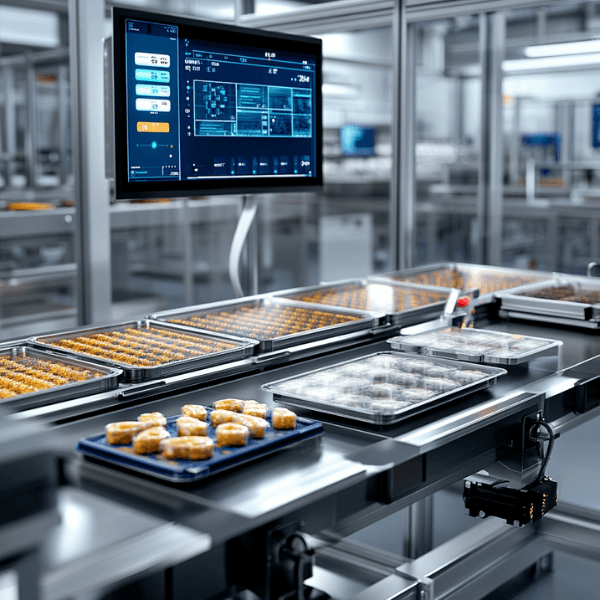
Gain Flexibility with Remote Operations Using PLCs and HMIs
A mid-sized plastics manufacturer in Germany cut maintenance costs by 50% and saved $30,000 annually by switching from standalone systems to an integrated PLC-HMI setup (Source: Schneider Electric Savings Report). Operators also optimized equipment usage, increasing production output by 10%.
Key Benefits:
- Remote access: Monitor and adjust operations from anywhere.
- Operational flexibility: Reduce reliance on on-site personnel.
- Enhanced monitoring: Stay in control even when off-site.
Once talking with a supervisor, he said, “During lockdowns, I tweaked operations while having coffee at home. It was a lifesaver.”
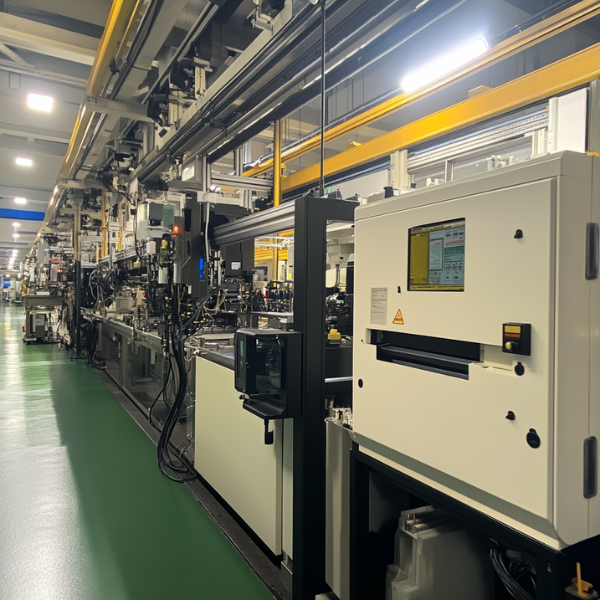
Future-Proof Your Business with Scalable PLC-HMI Systems
A pharmaceutical plant added two production lines over a weekend after adopting a scalable PLC-HMI setup, cutting downtime by 80% compared to their previous integration strategy (Source: ABB Industry Report). This ensured they fulfilled an urgent $1.2 million order during peak demand.
Key Benefits:
- Seamless integration: Add new devices without major disruptions.
- Future-ready: Scale up to meet demand without overhauling systems.
- Market adaptability: Stay competitive as business grows.
Pro Tip: Choose PLCs with modular designs to enable easy hardware or software upgrades.
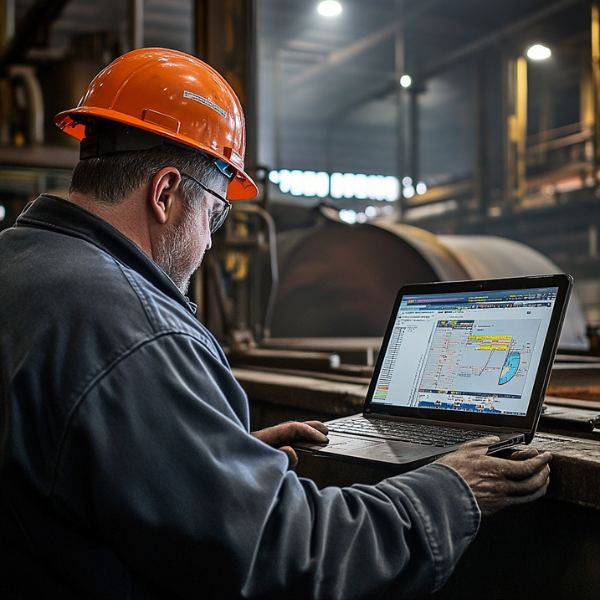
Address Common Integration Challenges with Expert Solutions
A manufacturer reduced project costs by 20%, saving $50,000, by using gateway devices to integrate legacy PLCs with a modern HMI system (Source: Siemens Industry Updates).
Key challenges and fixes:
- Vendor compatibility: Standardize protocols like OPC UA.
- Legacy systems: Use gateways to connect old and new.
- Cybersecurity: Employ encrypted communication and firewalls.
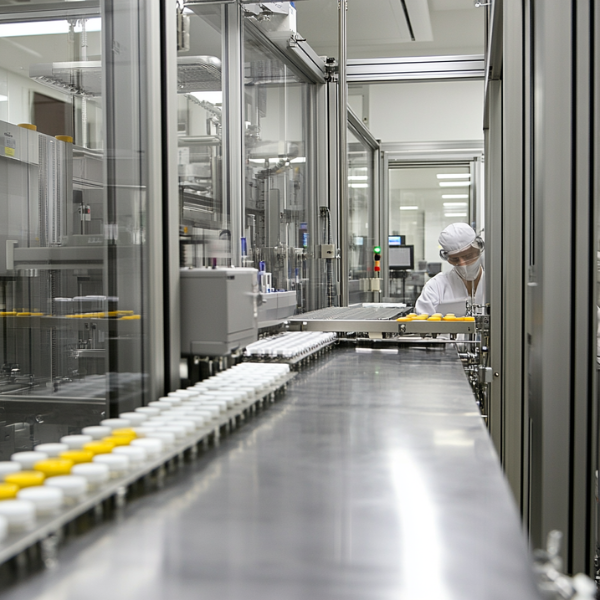
Plan and Execute a Successful PLC-HMI Integration Strategy
At an oil refinery, a poorly planned upgrade caused 25% more downtime than expected. For the next project, they developed a detailed rollout strategy, involving operators in testing and conducting phased training. This approach cut downtime by 35% and ensured a seamless transition.
Key Steps:
- Assessment: Evaluate existing systems and needs.
- Training: Prepare personnel before deployment.
- Testing: Simulate operations to catch issues early.
- Maintenance: Schedule regular updates and checks.
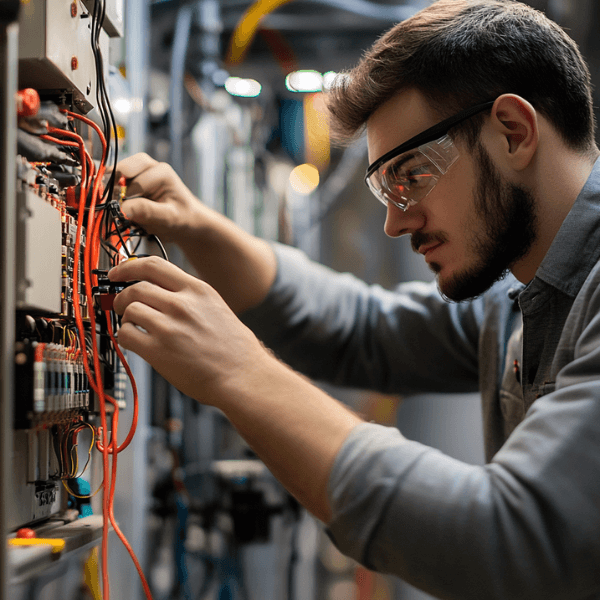
Conclusion
Integrating PLCs and HMIs doesn’t just cut downtime—it reshapes how businesses operate. With real-world applications and the right partners like Uni Regal Corp., this integration delivers measurable benefits, from cost savings to enhanced efficiency. Take the leap and transform your operations today.