Effective breaker maintenance [^1] prevents electrical failures and ensures safety. Without it, equipment lifespan shortens, and safety risks increase.
Proper breaker maintenance steps [^2] involve inspection, testing, and adjustments to ensure reliability and safety.
Understanding these essential steps will improve operational reliability and enhance facility safety.
Why is visual and mechanical inspection essential?
Neglecting visible signs of damage [^3] can lead to equipment failure. Addressing these issues early prevents costly downtime.
Visual inspections detect physical damage like cracks, rust, and loose connections. Inspect critical parts for issues.
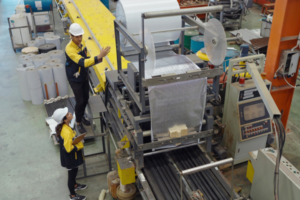
Key Components to Inspect
A thorough inspection should cover these areas:
Component | Issues to Look For |
---|---|
Arc chutes | Cracks, contamination |
Grounding/anchorage | Secure fastening |
All contacts | Wear, burns, loose connections |
Protection devices | Operational readiness, settings |
Prioritize cleaning and correcting visible defects to maintain performance.
How do testing and diagnostics improve performance?
Failures often stem from undiagnosed issues. Testing reveals hidden problems and ensures operational integrity.
Conduct tests like insulation resistance, timing, and trip testing every 3-5 years for MCCBs.
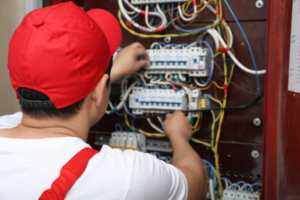
Common Tests for Circuit Breakers
Each test uncovers specific concerns:
Test Type | Purpose |
---|---|
Insulation resistance | Identifies potential breakdown |
Contact resistance | Ensures proper connections |
Over-potential | Checks dielectric strength |
Timing tests | Verifies proper response times |
By systematically diagnosing issues, facilities can prevent costly outages.
Why are lubrication and cleaning critical?
Friction and contamination [^4] hinder operation. Regular cleaning and lubrication [^5] ensure smooth functionality.
Lubricate moving components [^6] and clean contacts with a high-pressure air blast. Pay extra attention to oil-in oil circuit breakers.
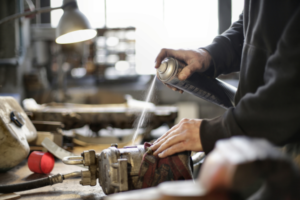
Cleaning and Lubrication Best Practices
- Remove dust and dirt from surfaces.
- Use the recommended lubricants for moving parts.
- For oil circuit breakers, replace or maintain oil quality.
These efforts reduce wear and enhance operational efficiency.
How do calibration and adjustment[^7] ensure accuracy?
Misaligned settings[^8] can cause malfunctions. Proper calibration ensures reliable performance and protection.
Calibrate interrupting structure mechanisms [^9] and adjust relay settings [^10] for short circuit and overcurrent protection.

Checklist for Calibration
- Test operational sequences for accuracy.
- Adjust breaker protection relays.
- Verify that mechanisms align with operational requirements.
Consistent calibration minimizes risks and optimizes functionality.
What are the benefits of operational checks?
Unusual sounds or incomplete operations signal underlying issues. Regular checks detect problems early.
Test manual and automatic functions, and listen for abnormal sounds during operation.
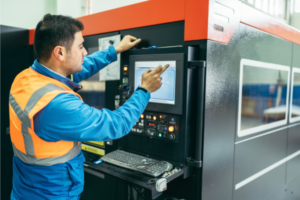
Operational Tests to Conduct
- Examine shunt coil, UV, and spring charge releases.
- Confirm the sequence of auto/manual operations.
- Document anomalies for further inspection.
Operational checks ensure the equipment runs as intended.
How do insulation and wiring inspections [^11] improve safety?
Worn or damaged wiring [^12] increases the risk of faults. Regular inspections address vulnerabilities.
Inspect wires for damage [^13], conduct insulation testing [^14], and replace any damaged components [^15].

Wiring Inspection Insights
- Look for frayed or worn insulation.
- Test insulation resistance.
- Replace damaged wires to maintain electrical safety.
Proactive wiring checks enhance reliability and prevent hazards.
Why consider environmental factors?
Environmental conditions directly affect breaker performance. Adapting maintenance to these conditions ensures durability.
Monitor temperature, humidity, and contaminants; adjust frequency in harsh environments.
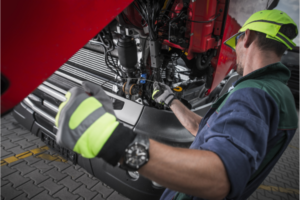
Adapting Maintenance to the Environment
- Increase cleaning and inspections in dusty or corrosive settings.
- Use enclosures for breakers in high moisture areas.
- Ensure proper ventilation in hot conditions.
Addressing these factors protects the equipment and extends its lifespan.
How do documentation and re-testing add value?
Tracking maintenance ensures consistency and identifies trends. Re-testing verifies improvements.
Maintain detailed logs, perform periodic tests, and consider third-party certification for quality assurance.
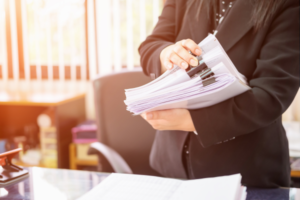
Effective Documentation Practices
- Record test results and maintenance actions.
- Track performance metrics over time.
- Use certifications to validate safety and reliability.
Comprehensive documentation simplifies audits and improves accountability.
Conclusion
Consistent inspection, testing, and adjustments ensure your facility's breakers remain reliable and safe. For any questions, don't hesitate to get in touch with Uni Regal Expert right away.